Shipping container storage isn’t just a trend—it’s a revolution in practical space management. Whether you’re a homeowner needing extra storage or a business streamlining logistics, these steel giants offer unmatched versatility. Let’s explore how to leverage them effectively without turning your property into a port yard.
Key Strengths of Shipping Container Storage
(1)Extreme Durability
Shipping container storage units are built to withstand harsh conditions. Their corten steel walls endure temperatures as low as -30°F and resist corrosion, pests, and fire. A standard 40ft container can hold up to 28 tons of weight—equivalent to 4 adult elephants—thanks to reinforced corner posts and steel frames.
(2)Weatherproof Design
The interlocking panels and welded seams create watertight seals. Unlike wooden sheds, shipping container storage solutions won’t warp or leak during heavy rains. For flood-prone areas, you can elevate units 12″ on adjustable piers.
(3)Vertical Scalability
Properly engineered shipping container storage stacks up to 9 units high. This maximizes space without expanding your footprint. A 2024 industry report showed that stacked configurations reduced land use by 62% compared to single-level warehouses.
(4)Custom Security Features
Steel walls deter theft, but you can add layers like crossbar locks (to resist angle grinders) or GPS trackers. Businesses using shipping container storage report fewer break-ins than those in traditional storage facilities.
Shipping container storage solves problems that traditional units can’t. If you are thinking about buying a shipping container for storage, don’t ignore these rules:
Do use containers for:
High-value equipment: Steel walls deter theft attempts
Hazardous materials: Ventilated 40ft containers safely store pool chemicals/farm pesticides
Avoid for:
Paper archives without dehumidifiers (rust risk)
Long-term electronics storage unless climate-controlled
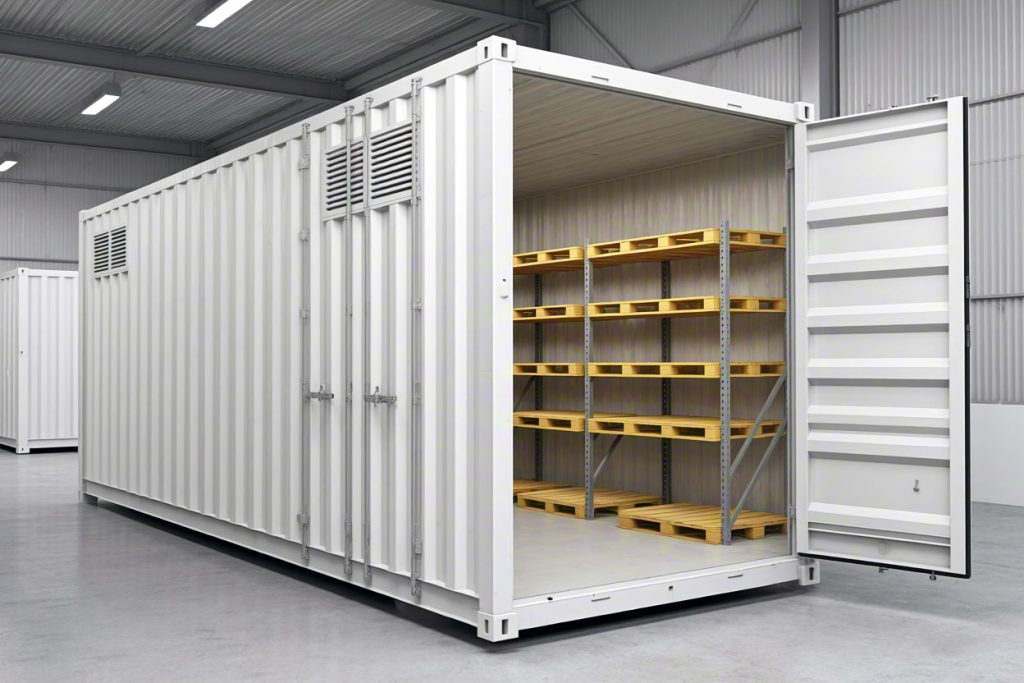
How Shipping Container Storage Works
(1)Passive Systems
Phase-change insulation: Wax-filled wall panels stabilize temps (68°F ±9°F)
Solar chimneys: $480 roof vents create natural airflow, cutting AC use by 35%
(2)Active Solutions
Dual-zone containers: Split 40ft units into chilled/+65°F sections
IoT monitoring: sensors track humidity/CO2 via smartphone alerts
(3)Disaster-Proofing
Flood-ready: Elevate 12″ on adjustable piers
Wildfire shields: Apply intumescent paint (withstands 1,800°F for 90 mins)
(4)Pest-proof
No gaps for rodents vs traditional wooden sheds
(5)Stackable
Up to 9 units high with proper engineering
But their real power lies in customization. A 2023 UCLA study found that businesses using shipping containers reduced storage costs by 38% compared to warehouse leases.
Your first step: Audit what you need to store. Containers work best for:
Equipment needing climate control (add insulation + HVAC)
Archive documents (use 10ft containers for easy access)
Retail inventory rotation (position near sales floors)
Shipping Container Storage Security Upgrades
Tier 1 (Basic)
Crossbar locks: 18mm boron steel resists angle grinders (5x longer than padlocks)
Motion lights: Solar-powered LEDs with 140° detection
Tier 2 (Advanced)
AI cameras: Reolink models detect license plates/faces
Geofencing: Get alerts if the container moves beyond GPS coordinates
Tier 3 (Military-Grade)
Vibration sensors: Text alerts if walls sustain impact
Faraday cage liners: Block RFID hacking of smart locks

Avoid These 7 Container Storage Mistakes and Troubleshooting Guide
(1) Ignoring zoning laws
Some urban buyers face fines for unpermitted placements.
Always:
Check setback requirements
Verify max height allowances
Confirm fire code compliance
(2) Choosing the wrong size
20ft containers: Ideal for 1,200 sq ft homes (holds 3-bedroom contents)
40ft high-cube: Fits forklift-accessed pallets (businesses)
(3)Skipping floor reinforcements
Standard marine plywood floors degrade under heavy machinery.
Reinforce with:
14-gauge steel plates (for automotive tools)
Epoxy coatings (chemical storage)
(4)Forgetting about condensation
Temperature swings cause “container rain.”
Combat it with:
Vented roofs
Silica gel packs (replace quarterly)
(5)Overlooking security
Basic padlocks won’t deter pros.
Layer defenses:
GPS trackers
Smart locks (app-controlled, audit trails)
(6)Climate Control Hack
Beyond Basic HVAC: Containers heat up 30% faster than buildings.
For temperature-sensitive items:
Passive cooling
Paint roofs with solar-reflective coatings (lowers internal temps by 18°F)
Install louvered vents for cross-ventilation
Active systems
Mini-split ACs (120 sq ft coverage per 12k BTU unit)
Dehumidifiers with auto-drain hoses (plumbing directly outdoors)
Pro tip: Use a wireless sensor to monitor conditions remotely.
(7)Financial Hack
Hidden Permit Costs: Texas requires windstorm certification, fire lane access, and so on.
Some states classify containers as “portable structures” to avoid property taxes. Consult local assessors.
Troubleshooting Guide
Problem: Rust streaks
Fix: Sand + apply cold galvanizing compound (matches original zinc coating)
Problem: Door jamming
Fix: Adjust hinge pins with a 1lb hammer + punch tool
Problem: Floor sagging
Fix: Weld cross members every 4ft
Future of Shipping Container Storage
(1) Leave expansion space: Position containers 4ft apart for future stacking
(2) Pre-wire for tech: Conduit pipes for future solar/security cameras
(3) Choose modular interiors: Bolt-down shelving vs welded units
Eco-Upgrades That Pay Off
Solar panels: A 600W system powers lights + security
Green roofs: Sedum plants reduce runoff + insulate
Rainwater harvesting: Attach 250-gallon tanks to gutter systems
The Future of Container Tech
Emerging innovations to watch:
Self-chilling containers: Phase-change materials maintain temps without power
Blockchain inventory tags: Track stored items via decentralized ledgers
AI damage predictors: Algorithms alert about corrosion risks
Shipping Container Storage: Your 8-Step Procurement Plan
(1) Test soil: Compacted gravel vs concrete pad requirements
(2)Get 3 bids: Compare container grades (CW vs WWT)
(3) Verify compliance: Ask suppliers for local permit templates
(4) Pre-install conduits: For future solar/security wiring
(5) Stage contents: Use pallet racks + vertical organizers
(6) Document everything: Photos pre-delivery avoid damage disputes
(7) Schedule maintenance: Annual rust checks + lock lubrication
(8) Plan exits: Resale value drops 30% after 15 years
Point of attention:
Measure your available space (add 3ft. clearance perimeter)
Get 3 quotes from local suppliers
Test ground stability with a percolation test
Containers aren’t magic boxes—they’re tools. Used strategically, they turn storage headaches into competitive advantages.
MEOX Professional Safeguards
At every step of your shipping container storage journey, MEOX delivers engineer-driven, full-lifecycle protection
Structural Integrity:
Certified structural engineers oversee every stage, from foundation embedment to stacking configurations.
Corrosion Protection:
Marine-grade coatings, ISO-certified and salt-spray tested, ensure durability in all climates.
Precision Quality Control:
Each unit undergoes rigorous inspections, with laser rangefinders ensuring dimensional accuracy.