If you’re considering a Shipping Container House in Australia, you’re not alone. Australia’s housing landscape is changing. With rising construction costs, climate challenges, and demand for sustainable living, shipping container houses are no longer a niche trend–They’re a smart, stylish solution.
What Are Shipping Container Houses?
Shipping container houses repurpose steel containers (typically 20–40 feet long) into livable spaces. Originally designed for cargo transport, these structures are modified with insulation, windows, doors, and utilities.
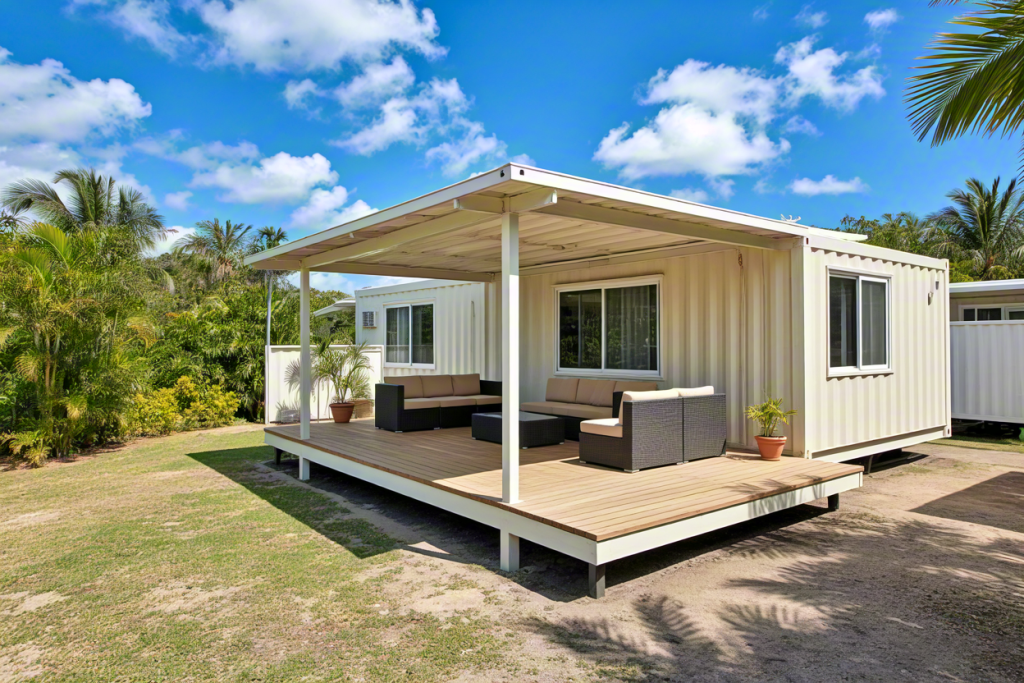
Why Choose a Shipping Container House in Australia?
(1)Speed to Move-In
While traditional builds take a year or more, your shipping container house will arrive in several months. Our modular system constructs 80% off-site while your land is prepared.
(2)Climate Resilience
Australian summers and bushfires demand toughness. Container houses meet standards using high-quality steel, thermal-insulated panels, and termite-proof foundations.
Key Challenges in Australia (And How to Solve Them)
(1)Extreme Weather Resilience
Australia’s climate demands specialized designs:
Bushfires: Opt for BAL-40-rated materials (non-combustible cladding, tempered glass).
Floods: Elevate structures on steel piers (meets Q100 flood standards).
Coastal Corrosion: Use marine-grade coatings (tested by CSIRO).
Your Action Plan:
Work with builders who pre-certify designs for your region.
Prioritize double-glazed windows (reduce heat transfer by 30%) and spray foam insulation (R5.0+).
(2)Council Regulations:
Container homes must comply with:
National Construction Code (NCC): Fire safety, energy efficiency, and structural standards.
Local Council Rules: Height limits (often 4.3m), setbacks, and zoning (rural vs. urban).
Your Action Plan:
Request pre-approved designs from suppliers to speed up permits.
Hire a private certifier familiar with container homes to avoid delays.
Designing Your Container Home: A Step-by-Step Guide
Step 1: Choose Your Layout
Single Container (20–30 sqm): Ideal for granny flats or holiday cabins.
Multi-Container (60–200 sqm): Combine 2–6 units for family homes.
Hybrid Designs: Mix containers with timber, glass, or stone for aesthetic flexibility.
Pro Tip: Visit existing homes via platforms like Open House Australia to gather ideas.
Step 2: Select Climate-Specific Features
Tropical North: Reflective roofing, cross-ventilation windows.
Southern Winters: Hydronic underfloor heating, R6.0 insulation.
Urban Areas: Soundproofing panels (reduce noise by 25dB).
Step 3: Budget Realistically
Allocate 10–15% of your budget for contingencies (e.g., soil testing, council revisions).
Compare quotes from 3–4 suppliers.
Common Mistakes to Avoid:
(1)Underestimating Insulation Needs
Poor insulation leads to condensation (common in coastal areas) and extreme temperatures.
(2)Ignoring Site Preparation
Uneven ground or poor drainage can cause structural issues. Always conduct a geotechnical survey.
(3)Choosing the Wrong Supplier
Verify credentials:
Licenses: QBCC (QLD), VBA (VIC), or equivalent.
Portfolio: Look for completed projects in similar climates.
Ignoring Sustainability Concerns:
Solar Integration: A 6.6kW solar system can power a 3-bedroom home, cutting energy bills.
Water Efficiency: Install rainwater tanks with first-flush diverters
Material Choices: Low-VOC paints
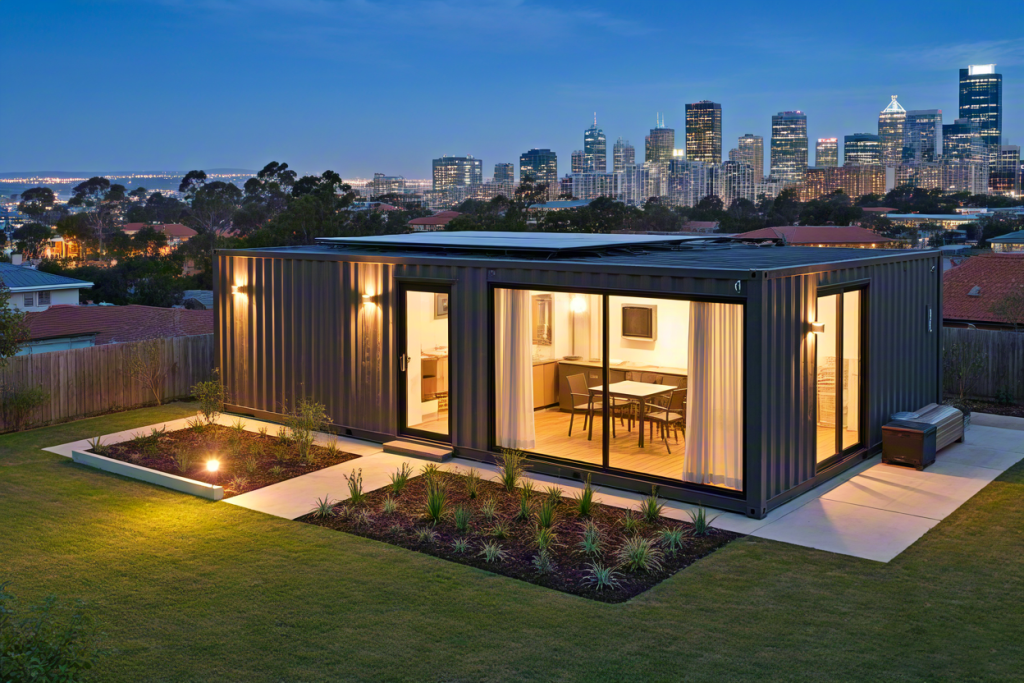
How to Find a Standout Shipping Container House Supplier
Building a Shipping Container House in Australia is an exciting venture, but finding the right supplier can make or break your project. With prices and quality varying wildly across the market, here’s how to identify a truly exceptional partner – one that turns steel boxes into dream homes without cutting corners.
(1)Demand Proof of Compliance, Not Just Promises
Every reputable supplier should openly share certifications like:
BV (Bureau Veritas) Certification, CE Certification, ISO 9001/14001/45001 System Certification;
Don’t settle for vague claims about “meeting standards.” Ask to see test certificates for corrosion resistance and load-bearing capacity. A standout supplier will have these ready for review and explain how their containers handle Australia’s harsh UV exposure – a key factor many overlook.
(2)Interrogate Their Thermal Performance Strategy
Shipping containers weren’t designed for human comfort.
Top suppliers solve this through:
1. Insulation systems tailored to your climate zone
2. Passive design principles like strategic window placement for cross-ventilation
Request case studies showing how their modifications maintain temperatures. Bonus points if they use non-toxic insulation materials – your health depends on this.
(3)Test Their Customization Expertise
True craftsmanship shows in how suppliers handle these challenges:
Structural cuts: Can they create wide openings without compromising integrity?
Local climate adaptations: Do they reinforce joints for cyclone-prone regions?
Material sourcing: Will they integrate steel for repairs?
Ask to visit the factory. Notice how they weld seams (continuous bead vs. spot welding) and treat rust-prone areas like corner castings. A standout supplier welcomes this scrutiny.
(4)Decode Their Warranty Fine Print
Many suppliers offer “10-year warranties” that exclude:
Coastal corrosion (within 50km of seawater)
Paint degradation from UV exposure
Modifications made after delivery
Look for warranties covering Structural integrity and Weatherproofing
(5) Council Approval Navigation Expertise
A truly professional supplier should be your guide through the maze of approvals:
Tailored Regional Strategies: Heritage conservation zones in Sydney vs. sandy soil regulations in Perth—each requires a different approach.
Real-Time Regulation Updates: Proactively informing you of upcoming regulatory changes.
Verification Methods:
Request to review a case study library of successful approvals from the past.
Ask, “What is the contingency plan if approval is denied?” A quality supplier should have a pre-review dispute resolution process.
Check if they provide a preliminary site compliance assessment.
You can check the Australian National Construction Code editions
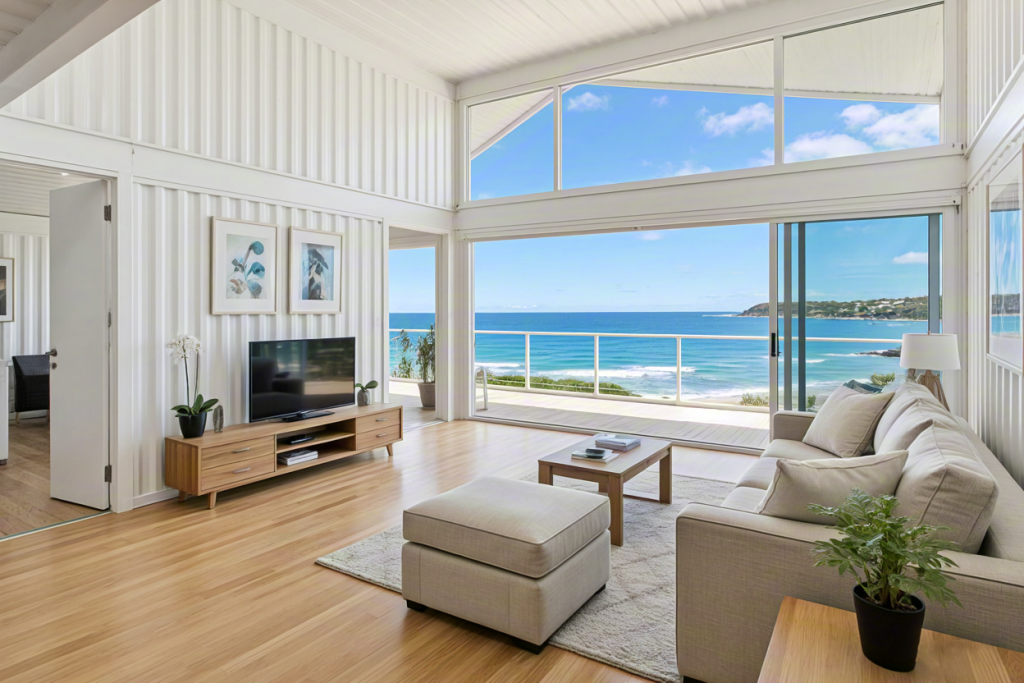
MEOX vs. Typical Container House Brands
Feature | MEOX | Other Brands |
Design Flexibility | Fully bespoke layouts + hybrid materials | Limited to pre-set container configurations |
Tech Integration | Smart house systems + solar-ready roofs | Basic electrical setups |
Warranty | 20-year structural | 15-year structural |
Real MEOX Projects: Australian Success Stories
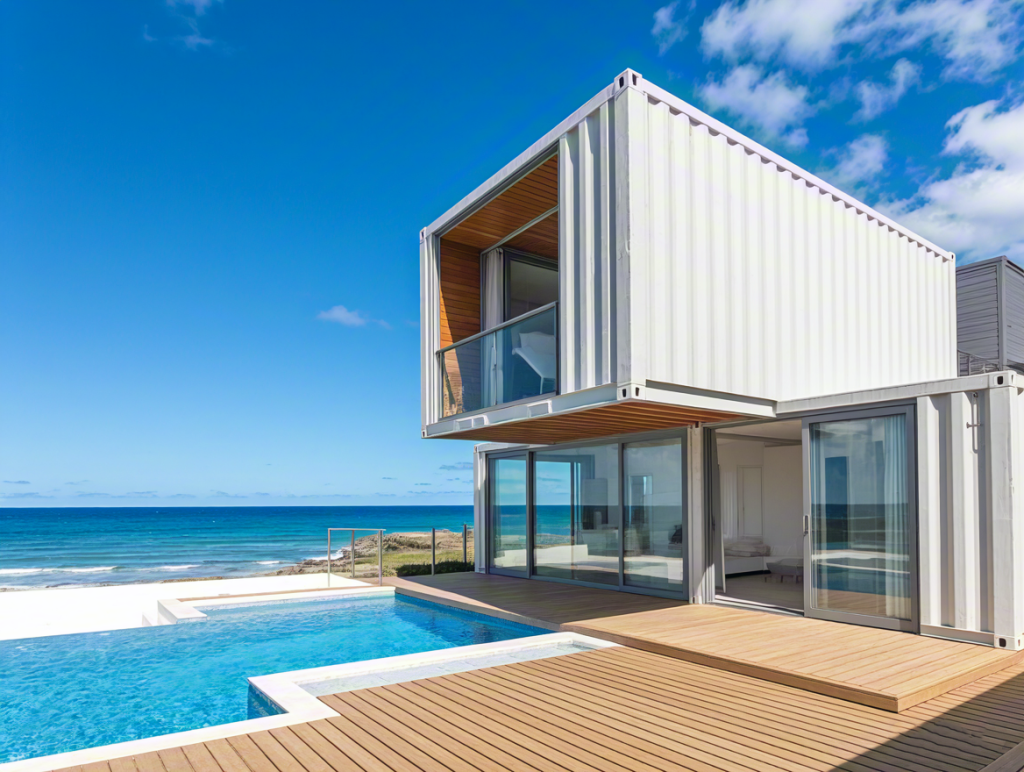
Case 1: Coastal Luxury
A family wanted a hurricane-resistant holiday house. MEOX delivered a 4-container design with:
Retractable glass walls.
Infinity swimming pool.
Off-grid solar + water systems.
Case 2: Urban Eco-house
A couple downsized to a 2-container house with:
Vertical gardens.
Underground rainwater storage.
Powerwall integration.
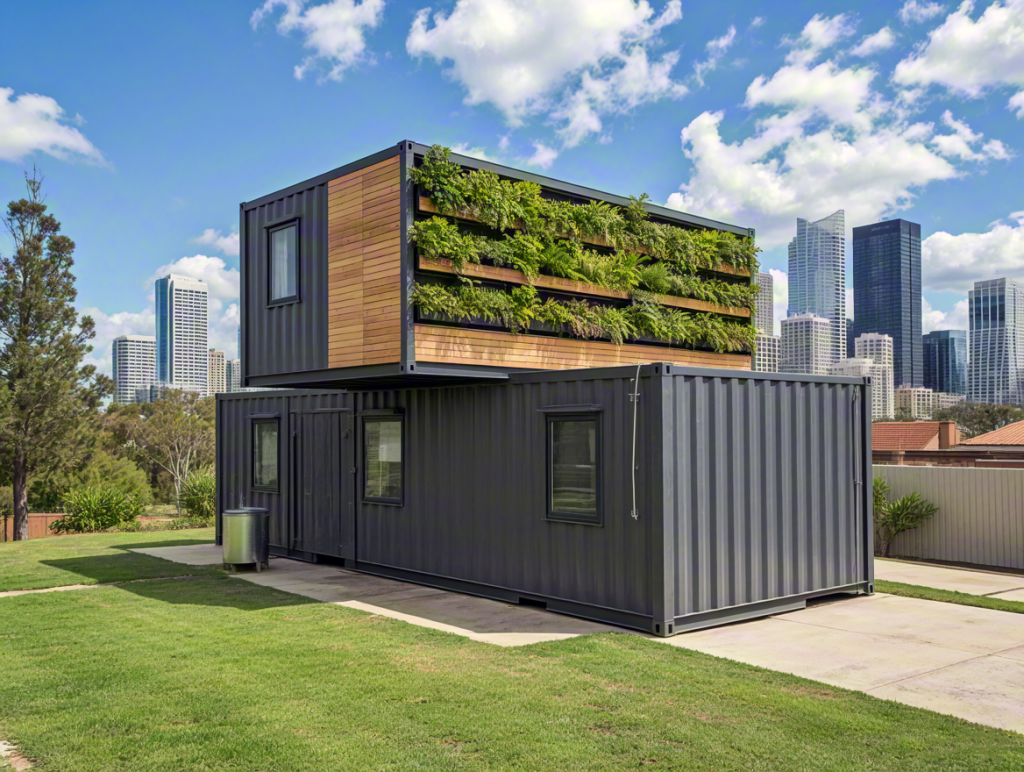
3 Reasons Australians Trust MEOX
25,000 sqm Factory: Precision builds using robotics and AI quality checks.
In-House Experts: Architects, engineers, and compliance officers under one roof.
Post-Build Support: Maintenance hotline and inspections.